Chainsaw mastery: Artist carves tree into gigantic human hand
Image is everything: Photographing your work
As Will Rogers said, “You never get a second chance to make a good first impression.” For woodworkers, we usually get only one chance to show our work to potential clients through our website and social media; to art, craft, and museum show juries; and to judges like those in the Veneer Tech Craftsman’s Challenge. So, if you want to make a good first impression, make sure your photographs are as best as they can be.
Quality of your photos can make or break the possibility of selling your work; getting accepted into craft shows; and winning awards. Of course, your first goal is to make beautiful and flawless woodwork, but your secondary goal should be to create stunning photos of it.
Although hiring a professional photographer is usually the best way to go, it can be costly. You might have to move large pieces to their studio or pay extra for them to come to your dusty shop. Set up can be time consuming. Photography is an art, and the field has its experts, but with available books, classes, and YouTube videos, you can get a decent education on taking good photos. And investing in a good camera and light boxes can dramatically increase the quality of your photos.
Start with basics
Luckily, with today’s affordable digital cameras (and even high-quality smartphone cameras), you can take good pictures with reasonable effort, expense, and practice. Start with the basics: Be sure to carefully clean your work, as any dust will show up in your photos. Take your time and schedule a half day (at least) for photography.
Be prepared to review test shots on your camera screen or PC. Adjust lighting as you go along. And while you’re set up, take a wide variety of shots so you can select the best ones later. Most cameras have a video mode, too, so take some short videos of opening doors and drawers, and move around the entire piece.
Lastly, take a shot with you in the image, take a formal one and a fun, crazy one. Don’t use them for jury or award submission; you can be disqualified if you include your face or name in the shot. But fun shots are great for your website and marketing collateral.
Here are some more specific tips:
Camera
Start with a digital device, either an SLR camera (Single Lens Reflex – where you see through the actual lens); a compact camera; or a smartphone. Next, connect it to a stable tripod, preferably with a remote control, as even pushing the shutter trigger can shake the camera and blur the image. I use my timer when shooting with my SLR and voice control with my smartphone. (My wife sometimes hears me yelling, “Cheese, cheese, cheese!” in my shop during a shoot.)
Background
There are two types of product shots: 1) studio with a white or neutral background; and 2) in-situ (“on site" or "in position,”) i.e., in a bedroom for a dresser or a hallway for a console.
Although in-situ shots can help give your work context, sometimes the surrounding background can take away from the piece. Avoid outdoor settings or piles of sawdust. Although they can be creative and great for your website, they are usually distracting for show or award applications.
Unless the work requires an in-situ shot to explain the function of the piece, or it’s installed, it’s best to shoot in a studio or your shop with a full background. Note: some publications like or require in-situ shots, so if time and funds allow, do both.
Studio backgrounds are typically created with a “seamless” (a large wide roll of paper) or fabric backdrop hung and curved down and under the work. Fabric drops are usually left wrinkled as it is hard to get them smooth. Fabric often comes with a molted print to help diffuse the look of the wrinkles, although sometimes patterns can be distracting.
I like to use a white backdrop because I can create a dramatic transitional shadow (a white to black gradient) by hanging a light-blocking panel above the work. A piece can also be digitally cut out and then I can create the background in Photoshop.
For larger work, limited space, and shooting in a shop, you can use bed sheets and/or white foamcore as a backdrop. You can overexpose these irregular backgrounds with additional lighting focused only on them, so they will appear smooth and all white. Don’t fret about dirt smudges or seams.
When you calibrate exposure time, start with the lights off. When taking shots, turn on the background lights and it will appear bright, smooth, and white. Using a shallow depth of field (wide lens aperture) will also put these imperfect backgrounds out of focus, which helps smooth them out.
If you don’t have a clean backdrop, you can also use a shallow depth of field, and set something consistent behind your work, like stacked wood or your row of hanging tools. Place your work as far away from the background as possible and keep the attention on the piece. Many smartphones have an automatic setting (live focus) or filter for this blurred background effect, and it works great.
Composition
Depending on the size of your work, capturing an entire piece can be a challenge. Start with a straight-on, overall shot, then take ¾ views from both sides and above. Follow up with more angles and details, with drawers or tops open, half open, etc. Include details, too, especially of any fine craftsmanship that can’t be seen in an overall shot, including fine joinery and inlay.
When you present your images on your website or in a jury/award application, consider how they will look as a grouping. Make sure the backgrounds are all the same, too.
Lighting
Most cameras have an auto white balance feature that keeps this step simple. The camera will calibrate on a white surface, then adjust and compensate for warm (yellow) or cold (blue) lighting. Light temperature can later be adjusted in post-production too.
A good intro lighting set includes a backdrop hanging rod system, and two side and one overhead soft box lights, all on adjustable tripods. I can set up my entire lighting system in 10 minutes.
Start by turning off all surrounding room lights and block out any window light, if possible. Next, I place my two soft light boxes on either side of the piece, pointing at a 45-degree angle toward the work, and lift them high enough to point downward, also at about 45-degrees. It’s important to use soft lighting and pay attention to shadows and reflections, which will be exaggerated in the photo. Your eye won’t be able to see this in real time, and reflection and glare can ruin a shot. Be sure to carefully review the image on the camera screen or better yet on a PC or tablet.
To help with glare, sometimes I shoot through a black wall of fabric or I place a frosted shower curtain in front of the lights to soften the white reflections on glossy finished pieces.
I also place white foam core on the floor just out of the camera frame tilted toward the work to reflect ambient light and fill in shadowed areas. I use another single light, 45 degrees off the back, to accent the back edge, a technique called rim glow.
Good lighting is critical and can be time consuming. Look for hot spots, dark shadows, reflections, and glare, and move your lights around to soften them out. Take lots of pictures.
File saving and post-processing
Be sure to save your pictures in the largest file format that you can. High-end cameras allow you to save in multiple formats such as RAW, TIFF, and/or JPEG. (JPEG is a condensed format that contains all the information needed for editing, but each time you save a JPEG, you lose information, so avoid resizing and saving multiple edited versions.) Work in larger formats and then save smaller files for your website and submission to juries or judges. You never know, they might ask for a larger file for the cover of a magazine.
Knowing how to edit images in a software program like Photoshop is a good skill to have, but if you are not accomplished at it, avoid it or use it very sparingly. Judges frown upon touched-up images, especially ones that are poorly cut and pasted on a fake gradient background. Don’t do this. Really. Don’t.
With a little practice, patience, and a few tools (new tools!) you can show your work off with high-quality images that will make you stand out from the crowd and even might get your work on the cover of a magazine or win you the grand prize.
A waving Stars and Stripes in walnut, sapele, and maple
Steve Guenzel is used to challenges. His company, Advanced Stair Systems supplies stairs and handrails for custom projects in the greater Philadelphia area. “We specialize in creating reproduction handrails using the Tangent Handrail Method and 3D modeling, which is an art and science unto itself,” he said.
But he tackled a different kind of challenge when he started making flags that are made mostly of solid American hardwoods but look like they are flying in the breeze. “We have been making American hardwood flags for a few years now,” he said. “The original idea was a personal challenge to do better than a few that I saw on the internet. They make a stunning statement of beauty and patriotism.”
His most recent project really stretched the limits since the flag is 6 feet long and 2 inches thick.
“This particular flag is a lot larger than most flags we made previously and is 39”x 72” and 2” thick,” he said. “I had designed the waving profile a few years ago, and just had to modify a few things for the larger size. The stars are the greatest challenge, but I feel also they are the key element that had to have the right look to them. Getting the stars to a sharp point is difficult, and took a little trial and error, but in the end, I think we nailed it.”
The stripes are 3 inches tall with the white stripes crafted of hard maple and the red stripes from sapele mahogany. For the star field, they chose black walnut, using hard maple again for the stars.
“The stars are a little more than 2 inches point to point and ¾-inch thick, with care taken to align the grain correctly with the stripes,” he said. “They are cut out, and then inlayed into the walnut star field with a lot of precision, as any gaps or poor fits are extremely visible.”
Gluing up the parts of the flag requires three stages, then the whole thing is planed to the finish thickness of 2 inches.
The next step is what really makes the flag distinctive: carving the waves to make the flag look like it is flapping in the wind.
“The machining of the wave and the final cutout of the flag is done on our 22-foot CNT Motion CNC router,” Guenzel said. “For this project we used Aspire CAM software to program the CNC and Autodesk Inventor for the 3D modeling to get the wave just right.”
Guenzel says it is impressive seeing the flag take shape on the bed of the CNC.
“Watching the CNC cut the wave is amazing and is surpassed only by the spraying of the first coats of clear coat on the flags, and watching the true colors just pop,” he said. “This stage almost brings you to tears.”
For maximum effect, the flags use only the natural wood coloring.
“Cutting the waves across the wood brings out an interesting grain pattern and lets the natural beauty of the wood come out,” he said. “No stains are used on our flags, as the genuine tones of the wood are incredible on their own.”
This flag will be proudly displayed in the showroom at Advanced Stair Systems’ new shop north of Philadelphia. For more on the company, you can visit their website at advancedstairsystems.com.
Minnesota Tool Library donates student desks
With so many students not able to attend classes on site in schools during the pandemic, the Minnesota Tool Library launched a program to encourage woodworkers to build desks to be donated to needy students.
The Minnesota Tool Library is a member-based, volunteer-driven nonprofit that offers community access to tools and training for woodworking and DIY projects.

"Part of MTL's mission is to empower residents with access to tools, training, and workspace,” said Kate Hersey, executive director. “When it comes to distance-learning, there are a lot of variables, but we know that a desk makes a difference. As a community, we couldn't be more excited to put our resources and skills to use on this project and provide our kids and our community a Space to Learn."
The original goal of the Space to Learn program was 500 desks, but they built more than 600 desks and had volunteers replicate the project using MTL’s plans across Minnesota, in New York, Florida, and even in Nova Scotia.

The program was also inundated with thank you letters from teachers and students. “I just wanted to send you a big thank you,” wrote Ms. Mattlin from Jackson Elementary. “I checked in with E. today and asked if she got her desk. She was thrilled to tell me that she got it and ran with her iPad to show it to me. She has all of her school supplies tucked inside, and it was the most excited I’ve seen her in a long time. We appreciate you and volunteers!”
Materials for each of the desks averaged $20 to $25 and estimated building time was about four hours per desk.

While MTL has exhausted its funding for the project, the organization is still making available its plans for people who want to make desks on their own. You can get more information at https://www.mntoollibrary.org/.
Slideshow: Frank and Oak HQ gets a new look
Frank and Oak, a clothing retailer that prides itself on sustainability, looked to make eco-responsible choices when renovating its Montreal corporate headquarters.
The company worked closely with Imperatori Design, an architectural firm based in Montreal, to strike a balance between maintaining the atmosphere of the original workspace and improving the quality of life for its employees.
Imperatori’s design includes a main entrance and its adjacent showroom that introduces two zones. One is focused on social gatherings and the other zone - more quiet and relaxed - leads to the workspaces. Included is the creative workshop where designers are surrounded by textiles, sketches, and samples.
De Gaspé, a local custom woodwork firm that has made sustainability a core value, played an instrumental role in the final results. The company executed the custom millwork and built-in cabinetry and bookshelves mostly using Russian plywood.
The quality of their millwork is impeccable and they are masterful with millwork that integrates metal and wood,” says Chantal Ladrie, senior designer of Imperatori Design. “More importantly they are a local workshop and their work is very representative to the Montreal vibe in terms of design.”
Frank and Oak turned to office furniture manufacturer Teknion of Toronto for seating, tables, desks and workstations. Frank and Oak's re-done space also includes Teknion privacy rooms.
Custom walnut table features scaled 3D model of construction site
Wood from historic ships built into desks for VP, Navy secretary
Seeking to create two historic desks comparable to the U.S. President’s historic HMS Resolute desk, a team of Navy Seabees used parts of famous ships, including the USS Constitution, to build desks for the Vice Prsident and the Secretary of the Navy.
Timber from the USS Constitution was used to build the desk now used by Vice President Kamala Harris. Often referred to as Old Ironsides, the USS Constitution was one of the six first frigates of the U.S. Navy. It was launched in 1797 in Boston, Massachusetts. Today, 224 years later, the Constitution is the world’s oldest commissioned warship afloat, according to the U.S. Navy.
The team also built a desk for the Secretary of the Navy made of parts from the frigates USS Constitution, USS Chesapeake, sloop of war USS Constellation, and battleships USS Texas, USS New Jersey, and USS Arizona. The Seabees team was attached to Naval History and Heritage Command, located at the Washington Navy Yard, which is responsible for the preservation, analysis, and dissemination of U.S. naval history and heritage.

Former Secretary of the Navy, Kenneth J. Braithwaite, poses with Seabees during an executive desk presentation event at the National Museum of the U.S. Navy. The desk project was initiated to deliver a desk of comparable provenance, history, and heritage as the president’s HMS Resolute desk. (U.S. Navy photo by Mass Communication Specialist 3rd Class Randy L. Adams II/Released)
“It’s a huge opportunity to be a part of,” said Builder 1st Class Hilary Lemelin, assigned to USS Constitution. “It’s amazing to create a desk for someone who makes such large decisions for the country and Navy knowing they’ll sit there every day is huge. The importance of their job can affect everything we do. It’s a piece of history now.”
The Seabees constructed the desks in about seven weeks. Staining and applying finishing coats was the longest part of the process due to the 24-hour drying time between each finish coat.
They used wood, copper, and nails from Constitution, wood from Chesapeake and Constellation, steel plating from Texas and Arizona, and deck bolts from New Jersey. The Secretary’s desk was made primarily of salvaged excess wood and copper from Constitution, a small amount of donated original wood from the frigate USS Chesapeake, donated salvage wood from the museum frigate USS Constellation, donated metal from the museum battleships USS Texas and USS New Jersey and a relic from the battleship USS Arizona.

Builder 1st Class Hilary Lemelin, assigned to USS Constitution, speaks with Acting Secretary of the Navy Thomas W. Harker during a heritage desk presentation at the Pentagon in Washington D.C. (U.S. Navy photo by Mass Communication Specialist 2nd Class Alexander C. Kubitza)
The team left square-nail holes in parts of the panels to show they came from the planks of the Constitution and as a reminder that sailors served on it. The panels were a piece of history they didn’t want to cover up. Yet, these were not the parts of the desk that mean the most to Lemelin.
“In each desk, we built pen trays in the center drawer and SECNAV Kenneth Braithwaite has a note written in there with a piece of the Arizona,” said Lemelin. “That’s the biggest thing for me because every time they open that tray to sign an important document that could potentially change the Navy or the nation, I think I put that there for them to use. For me, that’s history and we’re helping whoever sits in those seats think about the immense weight they hold.”

“This was the highlight of my career for sure,” said Senior Chief Constructionman Noah Ziegler, assigned to Naval Computer and Telecommunications Area Master Station Atlantic. “We worked together every day and learned from each other while we made desks that I’m extremely proud of. Watching the way the team meshed and helped each other on top of knowing these desks would be used for many years to come, it was an awesome overall experience. Saying it was an honor is a significant understatement.”
Ziegler said the team constantly talked about how they could maximize the materials they used to capture the spirit of the old ships and all the sailors who served on them.
This masterpiece Biedermeier desk from 1840 contains 105 hidden drawers
Austrian carpenter Vinzenz Hefele built this Biedermeier secretary in 1840 as his masterpiece - something Germanic tradespeople must build to in order to attain guild membership. The purpose of the piece was to demonstrate Hefele's exceptional craftsmanship.
With more than 100 drawers - most of which are hidden and accessed via intricate, yet simple mechanisms - Hefele's secretary certainly does the trick.
The desk took more than a year-and-a-half to build. It's made of walnut and measures five feet tall and three-and-a-half feet wide.
Watch Johannes Ranacher, a conservator at Austria's Museum of Applied Arts (MAK), reveal the desk's secrets in the video below.
If you're interested in learning more about what it takes to become a master craftsperson in Germany, and more about what qualifies as a 'masterpiece', check out this excellent article from Core77: https://www.core77.com/posts/51480/What-It-Takes-to-Become-a-Master-Fur…
'The Trees' guitar is made of "mythological" tonewoods previously off-limits
A new guitar from Fender master builder Ron Thorn features quite the spectacular combination of wood.
Named 'The Trees', the custom-built Offset Acoustasonic features three kinds of premium tonewoods - all of which have mythological status.

Stradivarius spruce, a wood that originates from the Musical Woods in the Italian Alps, was used for the guitary's body. Trees in this region have been protected and off-limits for centuries. Thorn got his hands on some of the wood after a storm felled a few of the region's trees.
The mahogany used on the top was even harder to come by, says Thorn. It was taken from "The Tree" - a mythological piece of Honduran mahogany.
“In 1965, deep in the Honduran rainforest, a group of loggers came across a massive ten-foot diameter by 100-foot tall mahogany tree,“ he explains. “It was felled by axe, but landed in a ravine that proved too difficult an area to retrieve it from, so the loggers just left it and moved on.
“Fifteen years later, a sawmill owner rediscovered it, and upon closer inspection recognized its unique character and beauty. They had it cut into four sections to remove it, and once it got to the sawmill it finally revealed the most incredible figure ever found on mahogany.“

The final piece of wood is used in the guitar's neck. Also mahogany, Thorn says he's had the piece for 15 years. It was taken from a tree submerged in a Belize river for more than 75 years.
Thorn says the guitar is the highlight of his career. Check out his Instagram post:
Slideshow: Entries for the 2021 Veneer Tech Craftsman’s Challenge
To recognize excellence in veneer woodworking, Woodworking Network presents the entries to this year's Veneer Tech Craftsman’s Challenge awards. The annual competition will accept entries until midnight, June 7, 2021 - so these are just the entries we've gotten so far.
The Grand Prize winner will receive $3,000 cash and other category winners will receive $1,000. In addition to the Grand Prize, the distributor for the winning entry will receive $2,000 and the distributor salesman will get $1,000 for supplying the veneer products or wood product application used.
Awards will officially be announced at the upcoming AWFS show July 20-23, 2021.
All projects must have been produced using natural veneer and wood product applications, but it doesn’t matter how much or how little of either is used. Whether it is furniture, cabinets, architectural woodwork, marquetry, special products or student work, all woodworkers need to do is demonstrate their craftsman’s touch. Also, it is not required that Veneer Technologies be the source of materials used to create the entry.
Note that there is a five-year threshold as all entries must have been produced no earlier than January 2016. Re-entries from previous craftsman's challenge competitions will not be accepted.
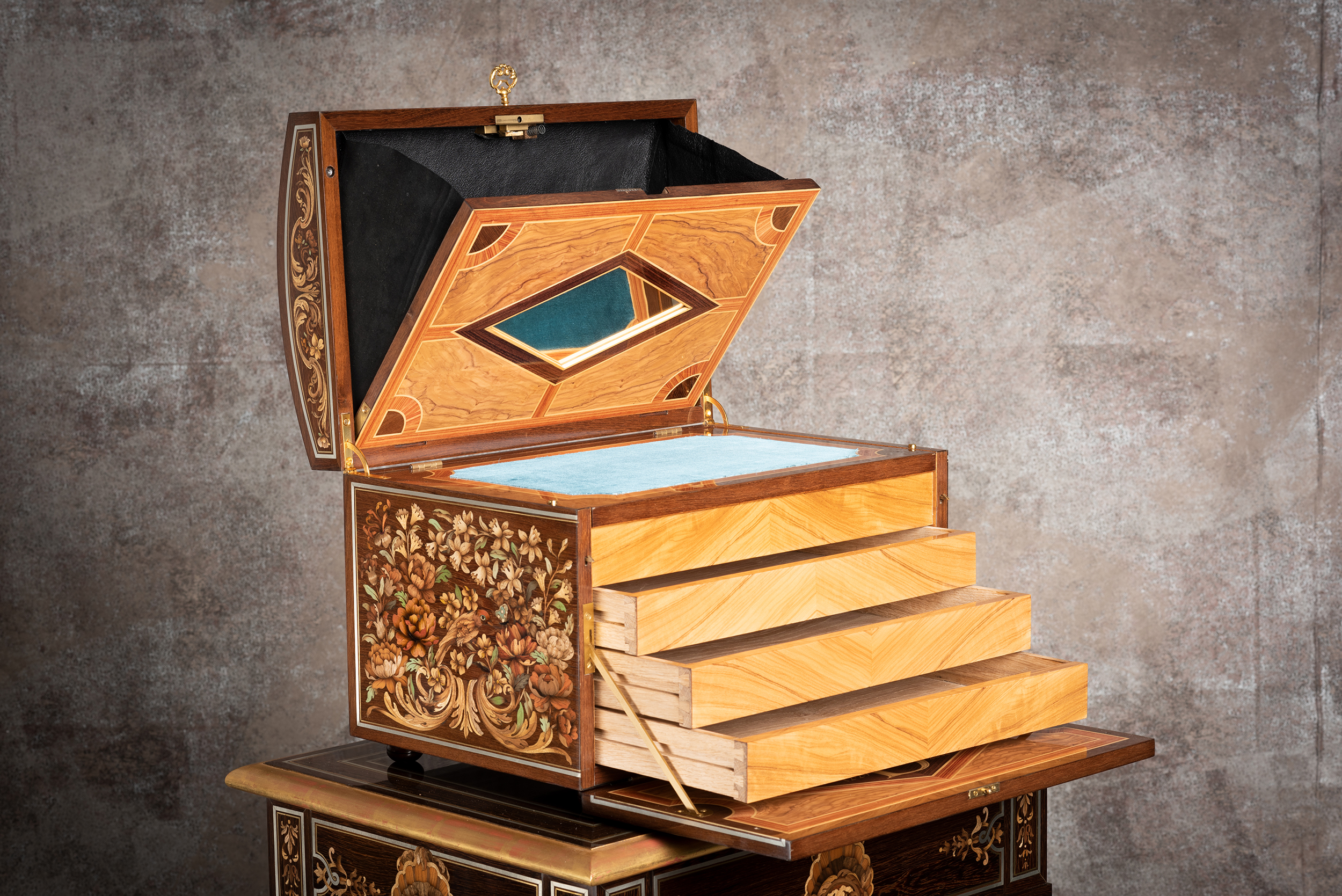
Last year's winner was furniture maker and marquetry expert Patrice Lejeune, who won for his "Trease Box III." Lejeune's box featured spectacular marquetry on the outside with intricate interior drawers and secret compartments throughout.
If you wish to enter this year's competition, you can do so below.

(Disclaimer: Contest entries displayed here have been submitted to the Craftsman's Challenge, but not yet verified by this year's judges and some may not meet the requirements to be accepted).
YouTuber expertly carves drivable Bugatti car from oak
Give Vietnamese YouTuber Trương Văn Đạo some wooden blocks, a chainsaw, a scalpel, and a drill, and he'll give you an expertly-crafted wooden Bugatti Centodieci.
Well, not you, rather - Đạo built it for his young son. Every part of the small, but to-scale model is crafted from oak. That includes the wheels, brake ducts, chassis, steering wheel, and body. The car comes complete with front and rear headlights, the Bugatti logo, and even a carved license plate.
An electric motor and two batteries serve as its power.

Đạo posted videos showcasing the build to his YouTube channel ND - Woodworking. Both part 1 and part 2 have amassed nearly a million views each. Check part 1 out below:
Other videos show off wooden carvings of sniper rifles, old school phones, and Santa's sleigh.

If you're interested in another awesome wooden car, check out Joe Harmon's cherry on balsawood Splinter, which took over 10 years to build.
Wooden Minecraft diorama made of 750 individual blocks, took two months to make
Master woodcarver, YouTuber, (and comedian) Bobby Duke's latest creation is a diorama inspired by Minecraft.
"I've been seeing really cool things online. People creating these little Minecraft dioramas using paper," says Duke. "Basically, I wanted to do that, but I wanted to combine Minecraft with wood."
Minecraft is the best-selling video game of all time and currently has around 126 million active players. The game world is composed of rough 3D objects - commonly called "blocks." This gives the game a unique, blocky sort of look.
In order to make the diorama look like it came from the game, Duke had to achieve that look. He did it by making and gluing together 750 individual blocks of basswood, a painstaking process.
"We're just going to keep on gluing blocks together for another 100 years," he jokes in the video.
He used more than a thousand custom waterslide decals to give the diorama its color and design. He explains how he made them in the video.
The only part of the diorama that isn't made of wood is the waterfall, which was made using resin.
The diorama and video took two months to complete. The video has picked up more than a million views in less than a month.
It's easy to see why Duke has one of the biggest woodworking-related channels on YouTube, with 4.3 million subscribers. His videos are well-edited and show off his brilliant work. But his success to me seems to be primarily due to his personality. You'll see what I mean while watching one of his videos.
You'll certainly be entertained.
Deadwood “waves” dash across a German forest
GERMANY - German photographer Jörg Gläscher spent five months in a secluded forest near Hamburg making waves.

Gläscher gathered enough deadwood to make nine waves – the largest of which spans 13 feet high and nearly 30 feet wide.

Gläscher was inspired by COVID-19 – specifically the fear of the second wave of COVID that hit Germany last fall. He told Colossal magazine that he was thinking about the total and absolute power of nature, which “brought one of the richest countries in the world to a complete standstill.”
Let us know what you think in the comments.
New product opens door for 3D printed wood items
A new product and process is changing the perception of 3D printing and expanding design possibilities for making things out of wood with no waste.
Called Forust, the new product was developed by a 3D printing technology company based in Boston called Desktop Metal. It uses sawdust and adhesive in a computer-driven process that can create wood parts without waste in design configurations that are difficult to impossible to achieve with conventional subtractive woodworking procedures.
One of the co-inventors of the process recently talked at length with us about the product, process, and possibilities of this new technology. Ronald Rael is a professor of architecture at the U.C. Berkeley College of Environmental Design. He says the driving force behind development of Forust has to do with creating a more sustainable wood manufacturing model, but it also can solve a host of wood manufacturing challenges from historic restorations to creating luxury wood products to whole new products that have yet to be dreamed up.

About the process
Rael says the process used to create Forust is very different from the common conception of 3D printing.
“Maybe many of your audience members have heard about 3D printing and think about plastic squirted through a little nozzle, and sometimes there’s an introduction of different kinds of materials like metals or woods with that plastic, but our process is very, very different,” Rael said. “We use reused and upcycled sawdust, so we’re taking the sawdust powder and we’re spraying it with a biodegradable and non-toxic adhesive to stick it together, so we’re reconstituting sawdust to create larger wood products.”
Rael says the process used is actually not new technology, but applying it to create wood products is a new application that expands the potential of an older 3D printing process.
“The technology is a really interesting technology, and it’s one of the oldest forms of 3D printing.” Rael said. “It’s been around over 30 years. It something that just hasn’t used many different kinds of material technologies. One of our innovations is that we’ve been able to introduce a new type of material to the system.”

What can it do?
Rael paints a picture of using this technology to create “almost anything,” but it does have particular applications and design possibilities.
“It’s really up to designers’ imaginations, but we can imagine things like architectural products for interiors, any kind of wall claddings, surfacing, almost anything you can imagine, luxury interiors, consumer goods, furniture,” he said. “We’re starting from the particle of sawdust, and we’re able to imagine if you grow that particle, those particles of sawdust and adhere them together to make any shape, you can really make anything that you might imagine.”
One application includes reproducing historic mouldings without the need to create moulding knife profiles or machine any more than the exact amount of material you need.
“In a historic renovation, for example, you might have a particular moulding, and it might be rotted. So, there might be a very small section or something. So, you have to go through all this custom tooling to replicate it, and that can be very expensive,” Rael explained. “But today, you can actually take a 3D scan with your telephone, with your iPhone, your smartphone, and you’ll have an instant CAD file that you can deliver to us, and it’s ready to print.”

New kind of grain
The process creates its own kind of grain in the printed wood parts. A statement on the Forust website describes the result as “3D printed, digitally rematerialized wood, with grain that flows across the entire part and can be sanded and refinished.”
Rael describes the process in more detail. “Because additive manufacturing is layer by layer in the same way trees build up layers as they grow, there is a certain directionality to the material,” he said. “Those layers in some cases can emulate or appear to be like wood grain as if the product actually grew just like in the same way a tree grew. But we can do some very special things layer by layer as well, like we can introduce different colors into the layers.”
3D printing technology even can be used not only to print the wood particles, but also the process can print images onto or even into the wood. “If you wanted to emulate a wood grain of any kind, you actually could do that within the wood structure,” said Rael.
This also presents finishing and pre-finishing opportunities, he said. Hyper localized color, even images could be applied within the wood product as part of the process. Rael compared it to applying a stain with a fine paint brush not only on the outside of a wood product, but inside, through the layers of grain or within the layers of grain themselves.
“What we’ve been doing so far is emulating different kinds of wood grains, but it could be actually anything or any image,” Rael said. “That opens it up to new kinds of possibilities of what applying finishing to a wood product might look like, and that’s yet to be discovered.”

Compared to natural wood
Just as woodworkers select particular wood species for their specific properties to best match them to a particular application, one naturally would want to know how Forust compares in strength and other characteristics to natural wood.
“(Forust) is an isotropic material and it has strength similar to if not greater in some cases than wood,” Rael said. “We can make it very strong. It has structural capabilities.”
He said they are limited by capabilities of existing machinery to print Forust parts. For example, don’t think of Forust as being the go-to product for large structural beams at this time.
“The beauty of it is that most wood products if they are assembled, are made of smaller wood parts, so we can manufacture many parts to produce larger structural items,” he said. “I don’t want to exactly say it’s like laminated timber, but in a way it’s laminated at the microscopic level. We can also laminate parts, but those parts don’t have to be flat like laminated wood products. They can be many different shapes and they can be joined together and connected and glued.”
One advantage Forust has over natural wood is greater dimensional stability that can even be enhanced by coatings applied during the printing process and after the part is printed.
“What’s interesting about that is that it’s infused into the layers, so it’s not just an exterior surface coating, it’s actually infused several layers in,” he said. “Rather than being sprayed on or painted as in a piece of furniture, a table, this is embedded much more deeply within the wood particles.”

Additive vs. subtractive
Understanding the potential of this new technology has a lot to do with understanding the differences between additive and subtractive manufacturing.
In traditional woodworking, the process is fundamentally subtractive, staring with trees, removing material to make logs, removing more material to make lumber, and continuing the subtractive process, removing even more material to dimension parts, create joinery, and shape parts for both decorative and mechanical purposes. In contrast, additive processes start from nothing and add material to get the final result.
“Because we’re growing it additively, we can make shapes and forms that could not be made possible with other forms of tooling,” Rael said. “That opens it up to new kinds of possibilities, maybe even products that are yet to be imagined.”
But it also requires thinking differently. Woodworkers will have to put aside their subtractive mindset to think additively to reap the full benefits of additive processes.
“I think in a certain way one has to abandon first what it means to subtract from wood and just to allow oneself to imagine what might be possible,” Rael explains. “For example, if you wanted to make a very large sphere or void inside a block of wood with a very small hole coming into it, I can’t imagine a tool that would do that very easily or if at all. But that could be absolutely possible with additive manufacturing.”
Rael thinks woodworkers’ understanding of manufacturing processes is tool dependent. “I think woodworkers or craftsmen begin to think based on the tool. They might think in terms of what does a chisel do or what does a bandsaw do or what does a CNC mill do,” he explains. “And craftspeople begin to think through those tools. I think one thing we have to recognize is this is a very new kind of tool, and that’s simply what it is. The tool allows us to produce new kinds of objects.”
Making parts from waste
Sustainability is clearly behind the development of Forust. Even the name of the product derives from that goal.
“We decided to go with Forust with U-S because we believe maybe we could preserve the forest for us, the planet and for the future,” he said. Rael emphasizes that Forust solves a major challenge in woodworking, dealing with large quantities of waste.
“If you wanted to make a hole in wood, you’d be removing all that wood, and you’d be left with a pile of wood dust, of sawdust, of shavings. We’re starting from there,” he explains. “So, when we make something, we’re not left with a pile of wood dust. We’re only left with the product, and that residual waste can be recycled back into our system and we can continue to make objects that way.”
Efficiency
Rael believes additive processes in general and the Forust product in particular add efficiencies to woodworking. Initially woodworkers could be attracted to a product that can be made without waste as an efficiency in itself, but Rael says the concept of efficiency should be broader.
“The efficiency of a product might be that it could be much more light weight or it could be a shell or it could be a three-dimensional object that would be very difficult to make that works with sound attenuation. I think the possibilities are endless,” he said. “A heavy piece of wood could be a light piece of wood. It can be perforated in ways that aren’t simply drilled through but in complex ways that are much more three-dimensional. So, the kinds of products that could be produced I think are yet to be discovered.”
Service bureau model
While many woodworkers will want to ask about buying machines to 3D print Forust products, the company is initially working from a service bureau model. That means wood manufacturers will send scans or digital files to Desktop Metal to have them printed in Forust material. The company wants to make software tool sets available so customers can work through additive design to achieve the parts they need. Rael emphasizes woodworkers need to approach all additive processes as a new tool for their shops.
“If we think about the moment that a particular woodworking tool was created like the CNC mill or the chisel or whatever, it expanded the possibilities of making,” he said. “We’re just going to expand the possibilities of making. We could think about traditional wood processes like wood restoration for example might play a role, but we can think about the future of wood products and those are yet to be discovered and those are going to be the most exciting discoveries that happen.”
You can listen to the full interview with Ronald Rael below.
Pumpkin carving woodworker style
With Halloween on the way, it’s an opportunity for many woodworkers to add their own special touch to the annual chore of carving the pumpkin.
I’ve been there, done that. Forget about the cute little tools they sell in the grocery store to carve pumpkins. I’ve got a whole shop of power tools that should make quick work of the job. My favorite is the cordless reciprocating saw. That makes the process efficient, and it is plenty accurate for pumpkin work.
But other woodworkers have other ideas.
Caleb Mean of the popular YouTube woodworking channel Mean’s Woodshop posted a satirical video showing how woodworkers typically over-complicate any project, including carving a jack-o’-lantern.
Some folks go in great detail to turn their pumpkins into a work of art. Others are more interested in speed and efficiency.
Flat River Rustics, a woodworking shop in Lowell, Michigan, has taken efficiency to the extreme and garnered more than 3.5 million views on TikTok by showing how to carve a pumpkin in just 15 seconds with a pressure washer. If you try to do this at home, be warned that pressure washers can be dangerous, and you could blow out the back of your pumpkin while carving the front. See the video below to watch how the Flat River Rustics folks do it.
Do you have special woodworking techniques for pumpkin carving? Share them with us!
Spooky carvings will haunt you
If you like your wood carving to be hauntingly inventive then Ohio-based woodcarver Josh Carte is your man.
Carte started out carving with a chainsaw and then refined his work by going with smaller subjects and more delicate tools. Today his specialty is wood spirit carvings that take natural wood and add faces and personalities. He especially likes to take advantage of natural shapes in the wood.
“It has taken me several years to figure out how to carve faces that I find pleasing, as I am very particular. Maybe even a bit nutty,” he says.
He spends a lot of time looking for unusual pieces of wood to use in his art.
“Venturing through the woods, searching for found- woods really tickles my soul,” he says. “Nature has such beauty to offer if only our eyes will see it. Gathering Pine knots, walking sticks and searching for burls has become a favorite past time for me.”
Some of the faces tend to the macabre, with ghoulish features, scary faces, and dangerous-looking teeth. He used a 9-inch high chunk of dogwood to make “Keeper,” a skull-based carving with beady eyes, jutting teeth, and long tongue.
“I used several different tools to make this piece,” he explains. “I began with a small chainsaw and worked my way down to a rotary bit that’s as thin as a needle. I finished this carving with spray urethane and thinned, oil paint.”

A bit more on the humorous side is “Monkey Business,” a toothy ape made from a gnarly spruce nodule. The creature’s pointy teeth are juxtaposed by his leering sidelong glancing eyes.
“This is a one-of-a-kind sculpture in a very unique piece of wood,” Carte says. “There will never be another creature just like this one!”

He transformed a piece of Big Leaf Maple Burl into “Igleador, a sharp-toothed, bulging eyed monster. It takes full advantage of the characteristics of the maple burl.
“This is a very unique wood, in that it has many pins and projections coming from it,” Carte says. “I love the crustacean-like look of this wood.”
You can see lots more of his creations in his Etsy store.
Laguna Tools offers CNC treat for Halloween
To celebrate Halloween Laguna Tools has posted a video demonstration of two of their CNC machines creating a Halloween scene, and they are even offering a download of the project file.
In the video, you can watch as a complete Halloween scene is created with the use of the Laguna Tools SmartShop SUV CNC router and the SmartShop Laser EX CO2 laser. Cut out silhouettes of eerie trees, creatures, and a graveyard set the tone for the backdrop as decorative jack-o-lanterns illuminate the forefront.
Follow the process as each outer border is routed by the CNC and the expressive faces on the pumpkins are laser cut by the EX. You can download the project file to do it yourself: https://bit.ly/3vtMt8m
VIDEO: Coolest Silverado ever
You can kick the wheels and slam the doors of the hand-carved Chevy Silverado. Oh, and it can tow too. In this latest design from Vietnamese YouTuber Trương Văn Đạo, he has created an intricately carved vehicle with moving parts, a slick interior, elegant engine, and a bed that can hold a ton. Made with chain saw and hand tools, this unit has it all. Priced to move.
Flexsteel invests in innovation
DUBUQUE, Iowa – Flexsteel Industries is intensifying its focus on innovation and design.
The number 28 company on the FDMC 300 list has made several recent moves signaling what the company calls a “major shift in product development strategy.” The company has elevated Don Bottorff to its newly created role of senior director of product innovation and design.
Bottorff was originally lured out of retirement from contract furniture specialist HNI Corp., two-and-a-half years ago to serve as director of products at Flexsteel. Now, according to Tim Newlin, vice president of product management, Bottorff is on the hunt for the “patentable, defined as new ideas and technologies not seen before in the furniture industry where we would own the intellectual property.”
According to a Flexsteel news release, language like that is rather unusual in furniture, a business more typically associated with an over-abundance of iterations of existing ideas, aka knockoffs, than “Eureka!” moments. “I call it the chase,” Newlin said. “Someone comes out with something, and too often, their competitors just tweak it. There's nothing fundamentally new. But you don't get a breakthrough product that way, and because of that, you only get small growth opportunities. Not big growth opportunities.”
Flexsteel said it is already well underway in a multi-year, multi-prong transformation in a bid to become a true omnichannel presence in the marketplace.
Changing the game
The key to the company's new product strategy is to seek out innovations that can be applied multiple times across multiple categories.
“Rather than product by product, Don is looking broader,” Newlin said, pointing for example to the company's Homestyle eCommerce business. “Say, you find a unique way to disassemble a sofa for shipping (or moving) that can be easily reassembled with a strong connection. Rather than use that to bring a single product to life, you can apply that innovation to multiple products currently in development. Patent it, and you have a differentiator and a right to win the marketplace that cannot be copied.”
As game-changing as this might sound for a company that aims its goods squarely at the broad middle of the market, Bottorff noted that Flexsteel was founded on innovation, specifically in seating suspension. Its proprietary blue steel spring™ frame, is in fact, a patented ribbon of steel that revolutionized upholstered furniture manufacturing when it was introduced in the 1920s and one that has not been duplicated since. Indeed, the blue steel seating system has been a true differentiator that thousands of consumers have been associating with quality and durability for generations.
“My job is really about problem-solving what the next legacy will be for Flexsteel Industries,” he said. “Certainly, it has to be authentic to the brand, so to be successful with the masses, to have the tremendous market reach, I'm sure it will have something to do with durable comfort at a great value. The biggest 'aha' moment I've had in the time that I've been with the organization is the simple fact that breakthrough innovation, and being in tune with the consumer, is not just a high-end, niche play.”
Coming from the contract furniture industry, which Bottorff described as “simply understanding the workplace and how to make people more comfortable and functional and therefore successful,” the executive is a fan of “human-based design.” Also known as human-centered design, it's a philosophy that empowers an individual or team to design products that address the essential needs of those who experience a problem. Interestingly, in Bottorff's mind, the most important word in that sentence is the team.
“I define myself as a product collaborator and I've made a career out of collaborating with cross-functional teams and talent to develop and launch relevant products for consumers. That's really what I'm about, and I'll be the first one to tell you that I've done nothing in my career by myself that was earth-shattering. Here at Flexsteel, I have three incredibly talented and gifted designers that I get to collaborate with to find better ways of executing meaningful designs, and while this is my second career to a degree, what I love is that demographically speaking, they represent the next generation of consumer. Who better to be designing furniture for the generation that we need to appeal to moving forward?”
Along with directing and developing internal design talent, Newlin said, Bottorff serves as the interface with designers external to the organization as well, “because you need multiple perspectives to make a thing great. He has always managed the inside design team and the relationships with designers when we look externally, and we do both, that's not new.”
What is a bit more unique is that while many in the industry tend to use words like innovation and design interchangeably (diluting the meaning of both), they are viewed as separate but equal disciplines here. “There needs to be a focus on both, and unless you have someone who owns it, which Don does, it's not going to get done every day,” Newlin said. “The fact that we have someone whose goals are built around that makes it more important to the organization as a whole, and it becomes a true core competency and a differentiator in the marketplace. Though I think from a product perspective we've always believed that, and we've had great designers working with us before, I don't think the organization recognized the unique nature of that skillset. Now, we're honoring it and leaning into it as a meaningful way to win business, and we believe it is a differentiator currently and will be in the future for Flexsteel Industries across all our brands.”
Thinking big
That last comment is particularly notable given that Flexsteel has had such a long and significant history in the upholstered furniture business because many tend to forget there is a lot more going on here these days. “Our team is designing not only Flexsteel soft goods and case goods, but also outdoor furniture, and across Homestyles, which encompasses all of our eCommerce products,” said Newlin. “A lot has to happen given that diversity of product across multiple brands.”
Indeed. To begin with, the company's designers needed a place that enabled them to approach their work in new ways. That led to the opening of a dedicated Innovation Center earlier this year, located about one mile, and a far cry, from the corporate headquarters. Positioned in the trendy Millwork District, an area that ironically enough was home to many of Dubuque's woodworking and industrial businesses back in the day, the design team now calls a historic, 1882 building home. The size of a city block, “the architecture is full of character, with exposed metal beams and brick, authentic factory carts and metal doors with all the original rivets and metal latches,” said Alek Eglinton, senior designer.
The evocative atmosphere of the space allows for creativity and collaboration in a way that was just not possible when the designers were housed at corporate. Said Eglinton, who spent seven years at the company before the shift to the new space, “Working in the corporate office kind of felt like being in a doctor's office, meaning it was sterile, with lots of glass and contract materials and finishes.”
While that “was great for business meetings and heads-down work, our leadership recognized that we didn't have a space to review furniture or build prototypes. Designers have different needs, and one of those is space to work through concepts.”
“When people think of design, they think of a sketch, or a concept,” Newlin said. “But it's the material choices, the color, the fabrics, all of the things that go into it and you need space to curate those items and make those choices.”
Part think tank and part concept modeling shop and part research and design lab, the Innovation Center “allows us to get messy,” Eglinton said, “with foam models and sawdust everywhere. Here we have the liberty and the tools and the space and the references to collaborate and think outside the box. Or, to work on modular projects since there's been such a need to flatpack almost anything since the pandemic. We can have furniture in here to look at for dimensions or be inspired by shape, or scale or fabric, to be hands-on, and to ask ourselves 'Is this human-based design, based on ergonomics and research, or is it just subjective? It's impacting our work from a creative standpoint and it's enabling us to get ahead of the market in developing design standards.”
Whiteboarding
As might be expected in a space devoted to innovation, one wall is devoted to whiteboards and cork boards where the designers tack up pictures, sketches, materials, and more as visual references. Given the speed at which product development and innovation are happening here, Eglinton shares that this invaluable visual tool is updated four times a year. “We do quarterly product meetings across all of our categories that bring the entire team together,” Newlin notes, “where we share our open projects for the next 12 to 18 months and Don goes through what needs working on from an innovation standpoint and how it might be applied.”
Of course, Flexsteel Industries is a global company with people working on projects not only in Dubuque but all over the U.S., Europe, Mexico, and Asia. For this reason, the company recently invested in a new software platform developed for movie production companies that replicates the whiteboard experience virtually and allows for collaboration in real-time with colleagues and partners around the world.
“Our team is spread out and we need to keep the creative juices flowing no matter wherever they might be,” Newlin said. “The technology makes projects visual so you can collect photos, any type of document, any inspiration, everything you love and put it up on the board instead of in file form. It's one thing to be on Zoom or Teams, but this is kind of a one-stop repository with everything on one platform. When the pandemic began, with everybody working remotely off-site, we tried to create something like it, but it was not an easy way to conduct business. Plus, having partners in multiple countries means communications can be limited to whatever is local, like WeChat. But after a meeting is over, where does the content go? You might have photos of an item or a video review, but this is a place for all that information to live and always be right at our fingertips.”
In other words, when it comes to innovative product development and design, Flexsteel is very, very nimble. “We're doing things differently and changing every day and we're going to start hitting price points that are lower, to start offering furniture that is smaller and easier to transport, and that is, at the same time, higher fashion and higher design,” Eglinton said. “There is such a receptiveness to new ideas, to ask, 'what if?'“
Bottorff agrees. “Never have I been around a group that is so focused on making things better, that is so motivated to have an impact on the consumers that we get the opportunity to serve,” he said. “It's incredibly unique, and frankly kind of rare.”
Expect it to pay off. “We're being thoughtful about the process, we're doing the research, and 100 percent focused on delivering the quality promise of a great, differentiated product that will be incredibly successful for the retailer or the e-tailer because of the work we put in upfront,” Newlin said. “At a time when the product development cycle has been disrupted by supply chain, just like manufacturing has, managing the process is tricky, but we think that taking this new approach to bringing a more meaningful product to the marketplace is the solution.”
Classic modern closet features LED lighting
Designer Lisa Plouffe, Closets Etc LLC, Pompano Beach, Florida, won the 2021 Top Shelf Design Awards Closet: Laminate Over 18 linear feet category with the “Classic Couture.”
This luxury closet design features a ton of modern touches from LED accessories and back panels to metal-framed glass shelves and quartz countertops.
Project details:
High gloss black and white thermofoil laminate and melamine custom closet.
Project construction:
Custom-designed and built thermofoil and melamine components with LED lighting throughout the closet system. Additional features include a floating island with inset drawers, under-lit LED lights, and a quartz top. Back-lit led panels behind shelving, LED hanging rods throughout, custom ladder and rail, 3-way framed mirror doors, and metal-framed glass shelves.
Project materials:
Thermofoil, melamine, powder-coated aluminum shelves, glass and mirror work, solid maple dovetail boxes with Blumotion soft-close slides, Alaco ladder, and railing system, LED rods, LED strip lighting, Tresco LED panels with acrylic covering, decorative hardware. Custom drawer inserts.
Software/equipment used
Standard shop machinery, Cabinet Vision CAD Software.
The 2022 Top Shelf Design Awards is open for submissions. Enter now for a chance to win.